Как делают швейные иглы?
Процесс производства игольной проволоки
Волочение проволоки, возможно, было изобретено в период с 1-го по 4-ый век нашей эры, что означает время, когда большое количество проволоки было необходимо для изготовления доспехов. Волочение первоначально производилось вручную посредством протяжки сырой или кованой проволоки через волочильную доску, которая забивалась острым концом в пень. В начале 14-го века для волочения проволоки впервые была использована энергия воды. Был разработан так называемый «Bankzogersbank-Zieherei» (в начале вид волочения). Здесь движение зажима осуществлялось с помощью коленчатого рычага, который приводится в движение кулачковым валом, соединенным с водяным колесом. Почти параллельно разработке «Bankzogersbank-Zieherei» (волочильного станка), производство основных материалов для волочения проволоки также изменились. Если прежде сырье для проволоки производилось при помощи молота, то есть ковались полосы прямоугольной формы, приблизительно 3 м в длину сечением 25×7 мм. Затем при помощи зубила эти полосы разделялись вручную на две или три полосы. После этого полосы нагревались и грубо ковались вручную. До середины 17-го века проволока производилась только из низкоуглеродистой стали.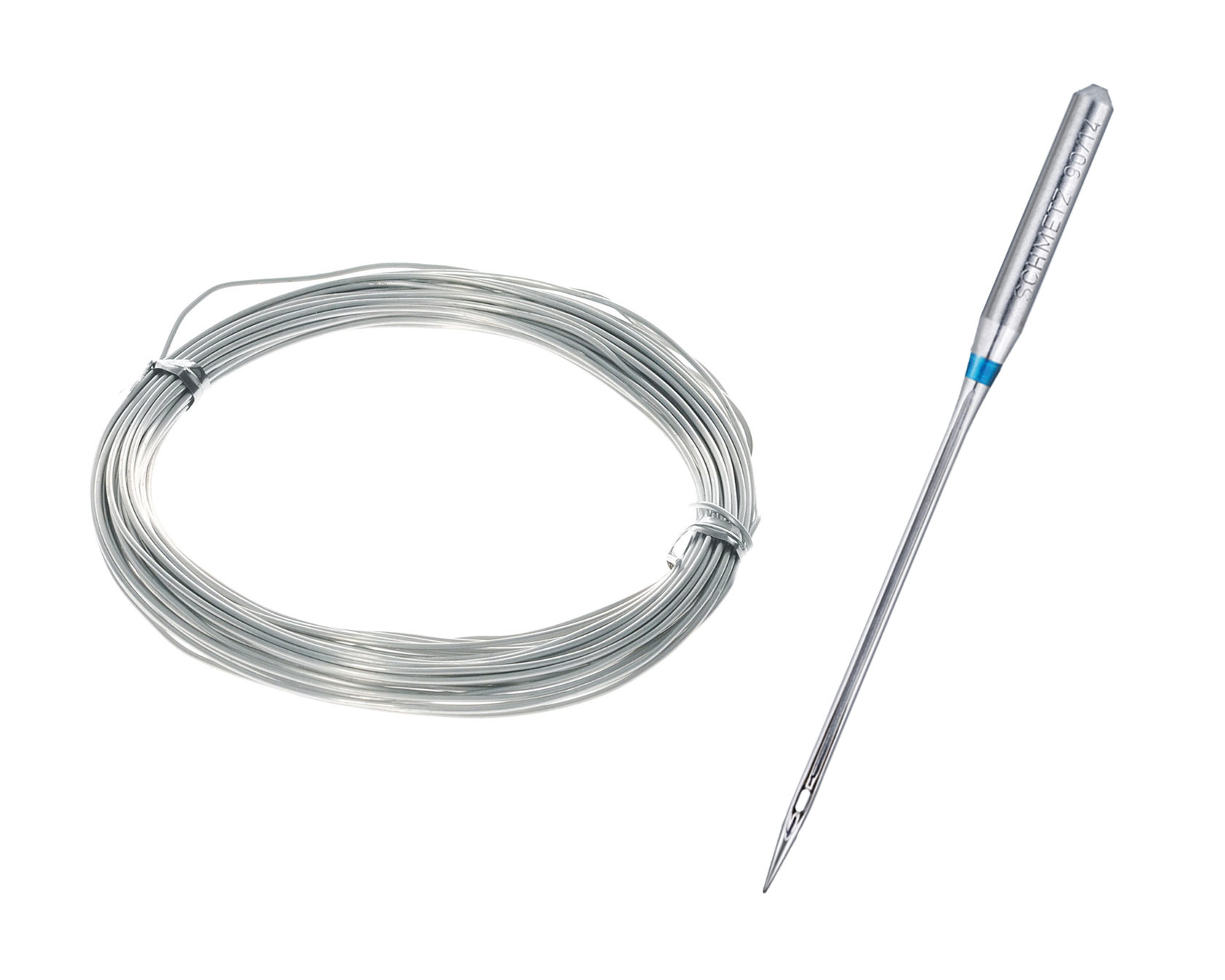
Использование смазки для уменьшения трения во время прохождения проволоки через фильеру было еще неизвестно; Из-за этого, изготовление проволоки с высоким содержанием углерода было невозможно. Первое использование смазочных материалов, и следовательно, первое производство стальной проволоки приписывается Иоганну Герлесу Альтену (Вестфалия / Германия).
После изобретения проволочно-волочильного стана в качестве основного материала для проволочноволочильных станов начали использоваться катаные прутки."Bank-zogersbank" был заменен на «волочильный станок», который отличался от так называемой вращающейся матрицы, которая приводилась в движение силой воды на протяжении веков, только по весу и диаметру и меньшим количеством оборотов, Таким образом катаные прутки могли быть уменьшены до диаметра примерно 3,5 мм. В дальнейшем волочение производилось посредством «промежуточного волочения» с использованием несколько меньших и более скоростных дисков. Это позволило получать проволоку диаметром примерно от 2,0 до 3,5 мм. Проволока диаметром менее 2,0 мм производилась на машинах тонкого волочения, конструкция которых была в основном идентична конструкции машин, упомянутых выше, но в них использовались более легкие и быстро вращающиеся диски. Для производства очень тонких проволок использовались еще более легкие станки.
В 1870-х годах в Англии была разработана новая система для производства стальной проволоки. Перед волочением проволока подвергалась специальной термообработке. В дальнейшем этот метод широко использовался для производства стальной проволоки во всех странах (поскольку он давал более высокую прочность в сочетании с отличной гибкостью).
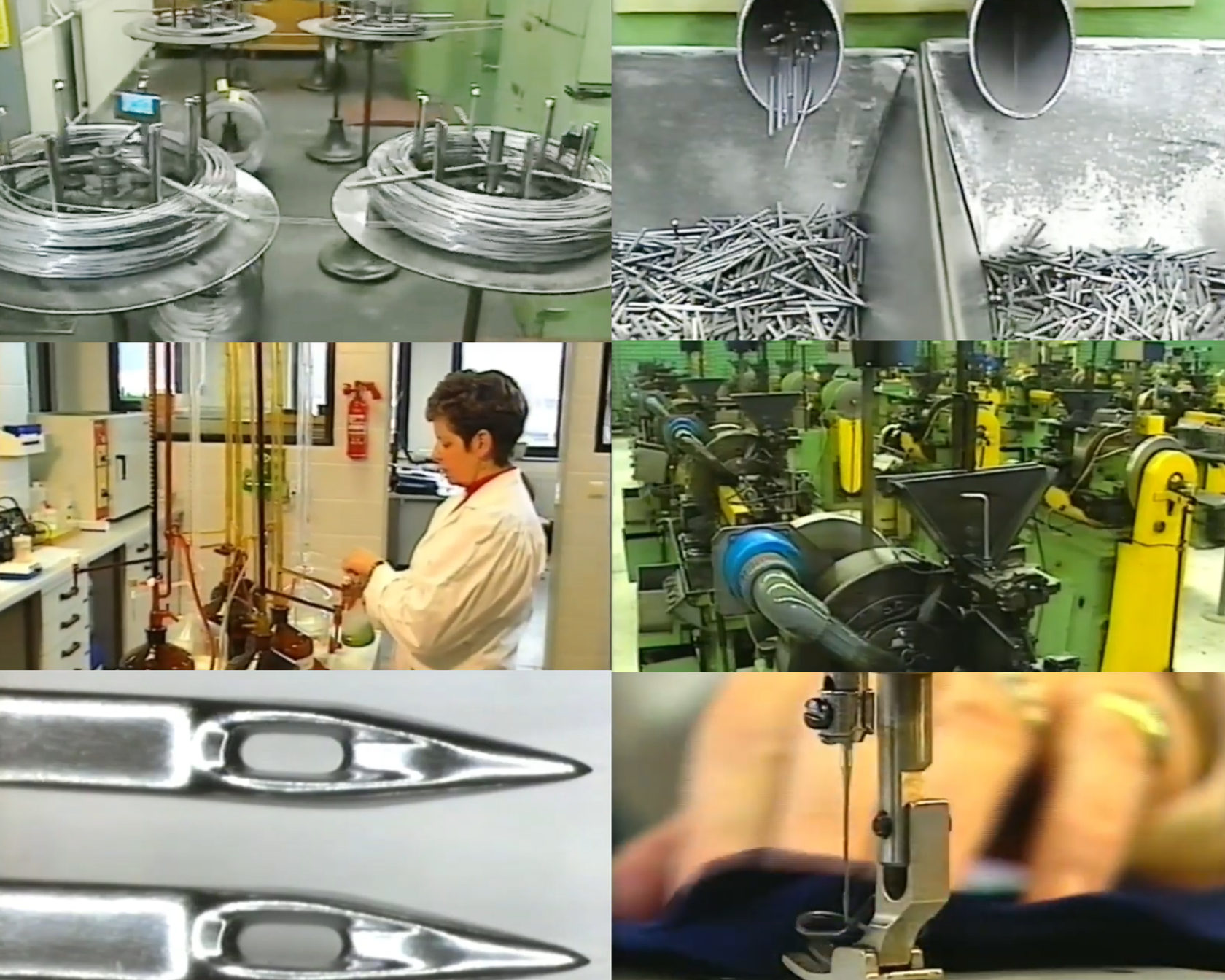
Для волочения проволоки в качестве основного материала, использовался катаный пруток, производимый на прокатных станах проволоки из слитков или заготовок. Наименьший диаметр прутка, который мог быть получен на обычном прокатном стане, составлял от 5,0 до 5,3 мм.
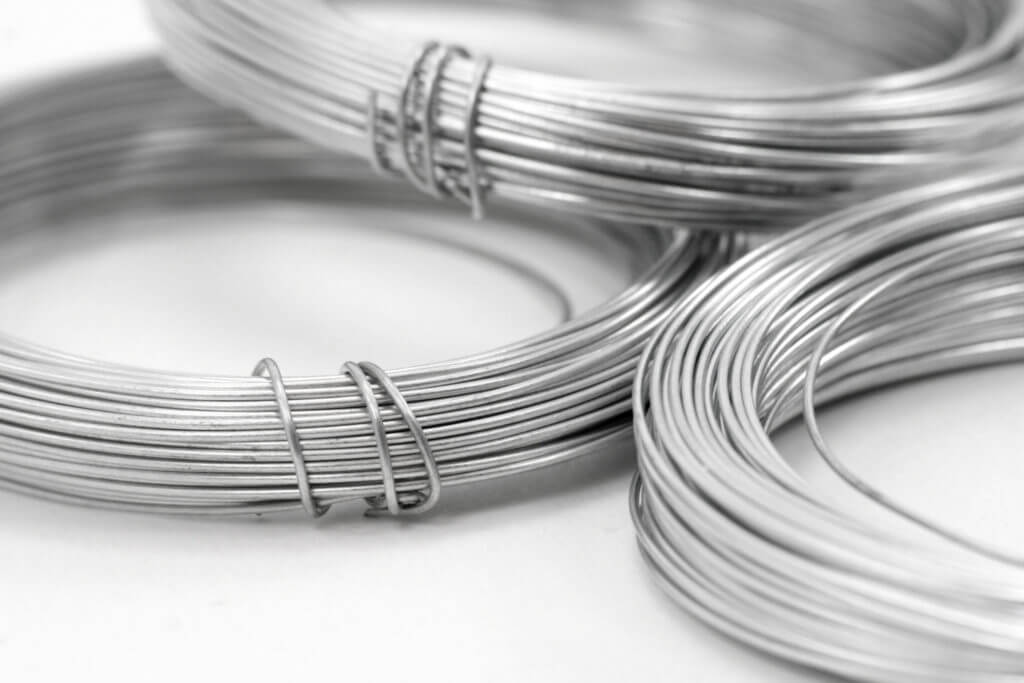
Значительные изменения в характеристиках стали имели место под действием растягивающего усилия в процессе холодной формовки. Они наиболее ясно демонстрируются увеличением прочности на разрыв и твердости, в то время как упругость уменьшается. Твердость затем снижается посредством отпуска. При этом восстанавливается имевшая место ранее гибкость и упругость. Точное изменение характеристик зависит от химического состава стали, особенно от
содержания углерода, а также от ее внутренней структуры, температуры и продолжительности отпуска и скорости охлаждения.
В зависимости от вида продукции, проволока, полученная на проволочно-волочильных станах, может быть классифицирована следующим образом: из мартеновской стали, томасовской стали, бессемеровской стали, тигельной стали и электростали. С количественной точки зрения, качества стали, полученной в ходе процессов Томаса и Сименса-Мартена являются наиболее распространенными. Игольная проволока, канатная проволока и рояльная проволока требуют расплава высокого качества. Следует ли отдать предпочтение мартеновской стали, бессемеровской стали, тигельной стали или электростали, зависит от особых требований к конечной продукции. Главными атрибутами бессемеровской стали являются высокая износостойкость, хорошая отделка после полировки и высокая гибкость. Когда тигельная сталь слишком дорога для той или иной цели, предпочтительной, как правило, является электросталь, благодаря ее высокой степени чистоты и, несмотря на ее высокие
производственные затраты по сравнению с сталями, производимыми, с использованием бессемеровского или мартеновского процессов, особенно когда требуется высокое качество.
Весь секрет в проволке
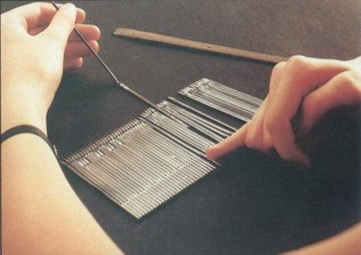
Всеобъемлющие и тщательные испытания материала, используемого для производства игл, является абсолютно необходимым. Они проводятся в испытательной лаборатории SCHMETZ, сначала, после поставки рулонов проволоки, затем во время производственного процесса и, наконец, на готовых иглах. Исследования материала можно разделить на три основные группы:
1 — Механические исследования и испытания
1.1 — Измерение диаметра проволоки
1.2 — Определение прочности на разрыв
Из всех процедур испытаний, применяемых к растягиваемым материалам, испытание на растяжение по-прежнему остается самым важным. Чтобы получить значение предела прочности материала (игольной проволоки) на разрыв, образец должен быть испытан до разрушения. Поведение материала во время испытания на растяжение дает дополнительные параметры свойств удлинения материала, например упругости и уменьшение площади сечения в точке разрыва.
1.3 — Определение поверхностных дефектов.
Кусок исследуемой проволоки скручивается вокруг ее оси несколько раз в обоих направлениях с помощью крутильной испытательной машины. В ходе испытаний, при разрыве проволоки открываются и становятся видимыми любые скрытые включения, в основном оксид железа в виде прокатной окалины.2 — Химические исследования и испытания
Они служат, чтобы определить содержание углерода в игольной проволоке для контроля, наблюдения и регулирования процесса закалки; проводится анализ защитного газа, используемого при закалке игл.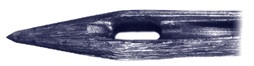
3 — Металлургические исследования
Металлургия занимает важное место в спектре процедур испытаний металлических материалов. Задачей металлургических исследований заключается в проверке внутренней структуры металлов их сплавов. Внутренняя структура и характеристики металлического материала тесно связаны, поэтому знание структуры позволяет сделать достоверные выводы относительно его пригодности. Холодная штамповка, механическая обработка и процессы упрочнения в производстве игл предъявляют особые требования к проволоке, близкие к пределам рабочих характеристик. Даже небольшие вариации таких характеристик, как размер зерен железа, тип и количество включений, количество и распределение карбидов железа, и характер поверхности могут помешать удовлетворительному производству игл. Детальное рассмотрение этих критериев приведено в следующих разделах.3.1 — Размер зерен железа
Размер зерен в проволоке изначально зависит от температуры разливки и условий охлаждения расплавленного металла, из которого она производится, но он значительно изменяется в ходе последующих операций пластической деформации, закалки и волочения. В общем случае, технологических применений требуется мелкозернистый материал, в котором различия свойств зерен в различных направлениях в значительной степени не проявляются. Если зерно становится грубым, происходит заметное изменение механических характеристик, в частности, снижение предела упругости и предела текучести. Это становится очевидным во время штамповки игольного ушка, поскольку пресс-форма «заполняется», и качество штамповки становится ниже стандарта.3.2 — Неметаллические включения
Каждая сталь имеет некоторое количество неметаллических включений, например, шлака,. Как правило, сталь должна содержать как можно меньше шлака, так как каждое включение является в некотором смысле трещиной или отверстием в стали, и действует в качестве внутреннего дефекта. Эти неметаллические включения также препятствуют удалению водорода и, следовательно, вызывают водородное охрупчивание. Во время хромирования игл на поверхности стали образуется атомарный водород, который легко проникает в сталь и растворяется в ней. В этой форме он, тем не менее, легко вытесняется в ходе последующего хранения или нагрева, то устраняет хрупкость, вызванную водородом. Если, однако, сталь содержит включения, трещины, поры и т. д., растворенный атомарный водород образует молекулы (молекулярный водород) в этих точках, вызывая дополнительные внутренние напряжения и повышенную водородную хрупкость водорода. Молекулярный водород не диффундирует легко через сталь и, следовательно, его последующее удаление представляет большую трудность.3.3 — Карбиды
Чтобы получить подходящую структуру для холодной формовки и закалки, игольную проволоку отжигают при докритических температурах. Области поверхностного растяжения, преимущественно представляющие собой составляющие перлита или сорбита слоев цементита, преобразуются в зернистую структуру. Зерна цементита вытесняются или поднимаются при холодной деформации и механической обработке (обжатии, штамповке и фрезеровании), но не срезаются инструментом, как это происходит при образовании слоистого цементита. Соответственно, количество, размер и форма карбидов имеют большое значение для рабочих свойств игольной проволоки. Если размер зерен очень мал, твердость стали увеличивается, и ее становится труднее обрабатывать. С другой стороны, если размер зерна большой, сталь становится мягкой и прилипает к инструменту в процессе резания. При сочетании значительной холодной деформации с чрезвычайно высокой скоростью резания о время резерования словия зменяются, а противоположные, например, слишком мелкозернистые карбиды склонны к налипанию. Таким образом, контроль размера зерен является критичным, и для обеспечения хороших условий фрезерования определенное количество карбидов на 1000 мкм2 не должно превышаться3.4 Обезуглероживание
Одним из самых серьезных дефектов, которые могут возникать во время отпуска или термообработки стальной проволоки является обезуглероживание поверхности. Иглы, сделанные из проволоки, имеющей пониженное количество углерода в поверхностных слоях, не достигают полной твердости, подобной твердости стекла в процессе закалки. Они имеют так называемую «мягкую кожу» и не могут быть использованы для шитья.